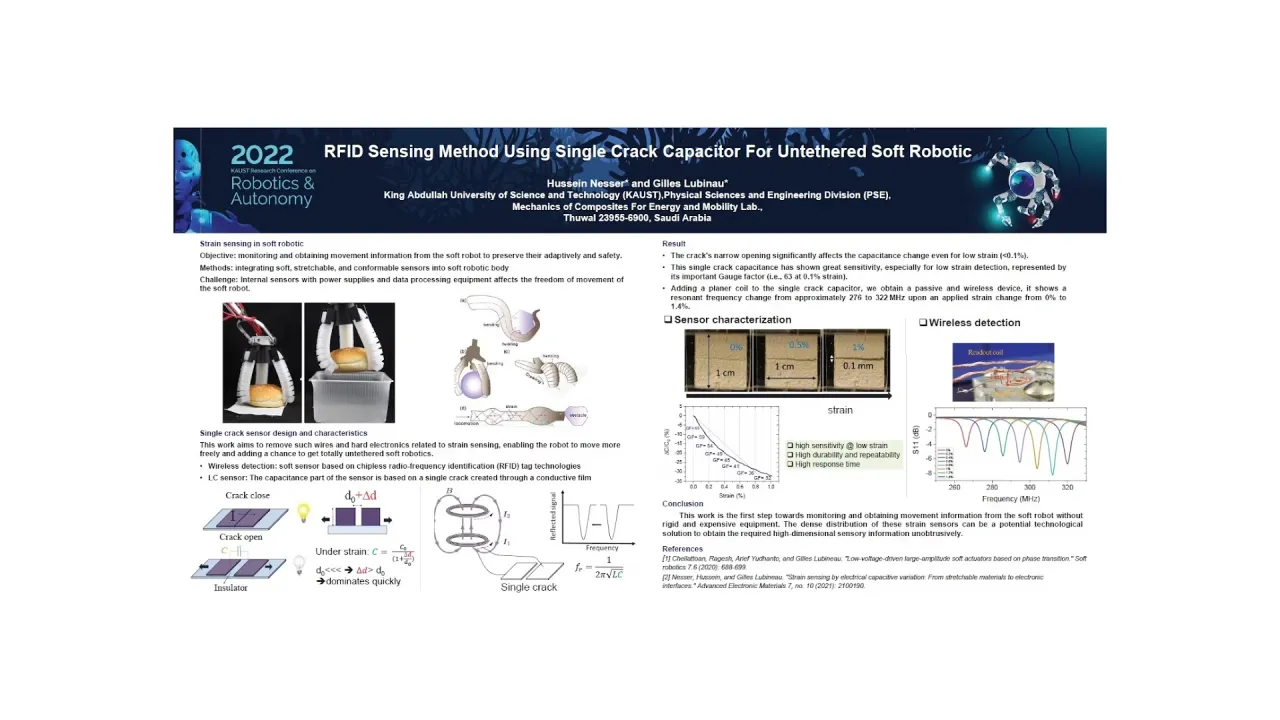
Dr. Hussein Nesser: RFID Sensing Method Using Signal Crack Capacitor For Untethered Soft Robotic
- Hussein Nesser, Mechanics of Composites for Energy and Mobility Laboratory, PSE, KAUST, KSA
KAUST Library
Overview
RFID Sensing Method Using Signal Crack Capacitor For Untethered Soft Robotic
Abstract
Due to their softness, soft robots are inherently safe and adapt well to unstructured environments. However, they can be prone to various damage types. Therefore, Soft robots require soft, stretchable, and conformable sensors to preserve their adaptivity and safety. Soft sensors can help a soft robot perceive and act upon its immediate environment. The concept of integrating sensing capabilities into soft robotic systems is becoming increasingly important. One challenge is that most of the existing soft sensors have a requirement to be hardwired to power supplies or external data processing equipment.
This work aims to remove such wires and hard electronics related to strain sensing, enabling the robot to move more freely and adding a chance to get totally untethered soft robotics. We present a wireless sensor that can be embedded, for example, in soft pneumatic actuators and observe very low strain (<0.1%) with high accuracy. This study fabricates and characterizes a new soft sensor based on chipless radio-frequency identification (RFID) tag technologies. We designed this sensor with a flexible capacitor connected to a coil to form an LC oscillator. An external coil can briefly power the LC device with electromagnetic waves to take sensor readings. This chipless RFID system can detect strain by following resonant frequency changes in response to an applied strain [1].
The capacitance part of the sensor is based on a signal crack created in a conductive film that forms a capacitor when the crack opens under strain. The advantage of this signal crack capacitance is its sensitivity, thanks to the crack's narrow opening, which significantly affects the capacitance change even for low strain (<0.1%). This signal crack capacitance has shown great sensitivity, especially for low strain detection, represented by its important Gauge factor (i.e., 63 at 0.1% strain). Adding a planer coil to the single crack capacitor, we obtain a passive and wireless device, and as such, it does not require a power supply and is capable of transporting data without a wired connection. This strain sensor is best understood as an RFID tag antenna; it shows a resonant frequency change from approximately 276 to 322 MHz upon an applied strain change from 0% to 1%. This work is the first step towards monitoring and obtaining movement information from the soft robot without rigid and expensive equipment. The dense distribution of these strain sensors can be a potential technological solution to obtain the required high-dimensional sensory information unobtrusively.
Brief Biography
Hussein Nesser is a postdoctoral fellow in materials science and multi-physics. He joined the mechanics of composites for energy and mobility Lab at KAUST in August 2019. He received his B.S. (2010) and M.S. (2012) degrees in condensed material and radiation from Joseph Fourier University, and subsequently obtained a Ph.D. degree in Materials Science and Electronics from the University of Bordeaux, France, in 2016. He worked as a postdoctoral fellow between 2017 and 2019 at INSA Toulouse, France. His research interests mainly focus on the electromechanical characterization of functional nanocomposites for applications that include actuators, sensors, and energy harvesters.